Quicktron X Ball & Chain
Repurchase is the Ultimate Endorsement: Well-known Snack Brand Deploys Over 200 Quicktron Robots
A well-known domestic snack brand based in Zhejiang adopted Quicktron's mobile robot solution many years ago. With an area of 36,000 square meters, the facility utilizes nearly 100 Quicktron second-generation Rack Transportation Robots "M100," along with automated conveyor lines, sliding sorters, elevators, stacking machines, and other logistics automation equipment, as well as WMS and WCS systems. This created a benchmark case for intelligent snack distribution centers, once becoming an innovative pioneer in the snack industry. As the return on investment exceeded expectations, the customer began replicating the intelligent distribution center model. For the second phase of the project, they chose to collaborate with Quicktron again, growing alongside the company.
Challenges And Objectives
Quicktron drives innovation, winning enduring trust worldwide.
The second phase warehouse is 1.5 times larger than the first project and uses Quicktron's third-generation M100 robots. To date, more than 200 Quicktron robots have been deployed. The entire warehouse consists of 2 buildings with 9 floors of flat storage, all using Quicktron robots to achieve high-density storage of goods. The Quicktron robots work in conjunction with robotic arms and elevator equipment to realize automated inbound and outbound operations. Based on scenario characteristics and user requirements, Quicktron provides the most suitable goods-to-person solution, greatly reducing the labor intensity for operators, saving labor costs, and improving overall operational efficiency.

Solution and Benefits
Robots Connect Each Process
First Floor Inbound Operations
When there are no empty rack stacks at the unpacking machine position, the upper-level system issues a rack stack transport task, and mobile robots deliver empty rack stacks to the unpacking machine. When the palletizing station has available space, the upper-level system issues an empty rack replenishment transport task, and mobile robots deliver empty racks from the unpacking machine to the palletizing workstation.
After palletizing is completed, the upper-level system issues a transport task to the inbound temporary storage area, and mobile robots deliver the loaded racks to the temporary storage area. When the storage area requires replenishment, the upper-level system issues transport tasks to the elevator buffer zone. Mobile robots deliver loaded racks to the elevator docking position, and the elevator transports them to other floors.

Storage Area Inbound Operations
After picking creates empty racks, the upper-level system issues tasks to the palletizing machine, and mobile robots deliver empty racks to the palletizing machine, which performs palletizing operations on the racks. For completed rack stacks, the upper-level system issues tasks to the empty rack stack temporary storage area. When the first floor requires empty rack stacks, the system issues transport tasks for empty rack stacks, and mobile robots deliver them to the elevator docking position, where the elevator transports empty racks to the first floor. Loaded racks are transported by elevators to various floors, and upon arrival, the upper-level system issues inbound tasks, and mobile robots deliver the racks to the full-pallet storage area in the warehouse, completing the inbound task.

Storage Area Outbound Picking
Based on inventory status and picking order requirements, the upper-level system adjusts racks from the full-pallet area to the picking area, with mobile robots completing the rack transport tasks. According to order requirements, the upper-level system dispatches racks to different workstations, including robot picking outbound workstations and manual picking outbound workstations. Mobile robots transport racks to different picking workstations as required by the system, and workstations complete picking operations following upper-level system prompts. The upper-level system simultaneously issues return-to-storage tasks, and mobile robots transport racks back to the picking storage area.

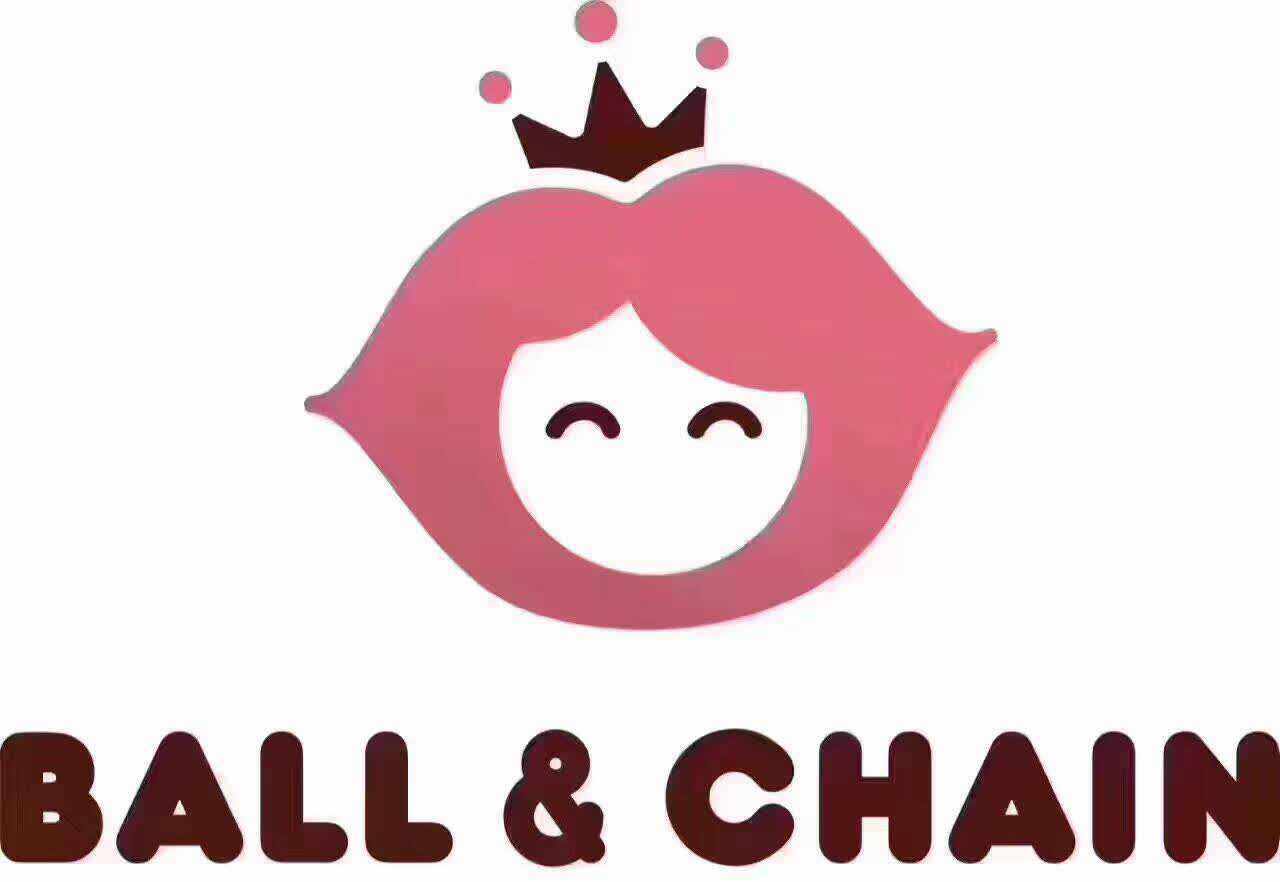
"Quicktron’s cutting-edge robotics solution has transformed our logistics and production processes at Ball & Chain. The substantial increase in efficiency, remarkable error reduction, and significant cost savings have had a tremendous impact on our operations. We are now able to deliver products more efficiently from raw material delivery to finished product storage, all while optimizing workflow and reducing labor costs."
Ball & Chain
Related Cases
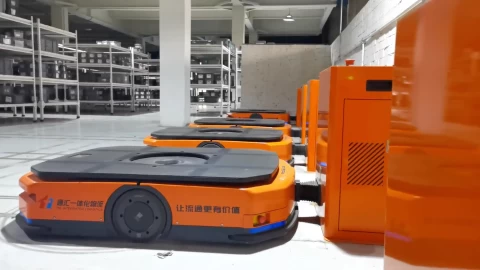
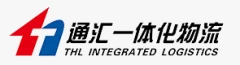
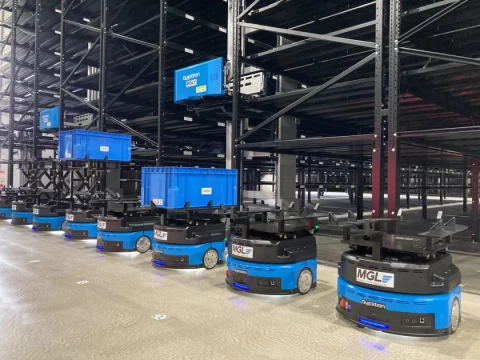
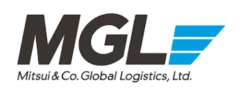
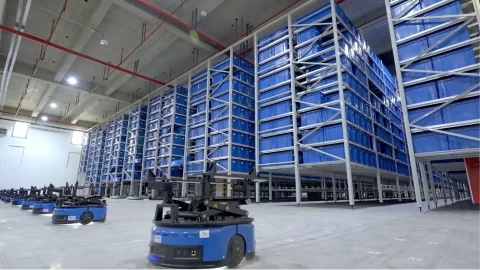
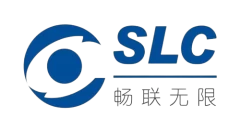
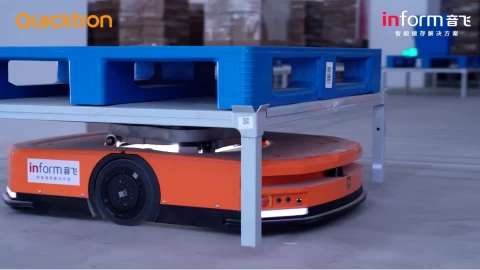
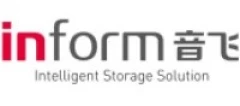
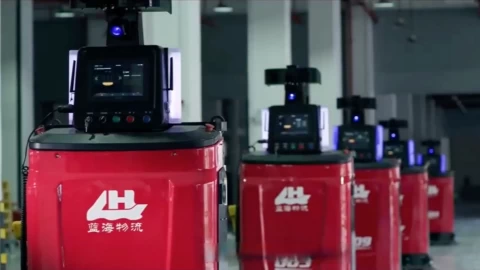

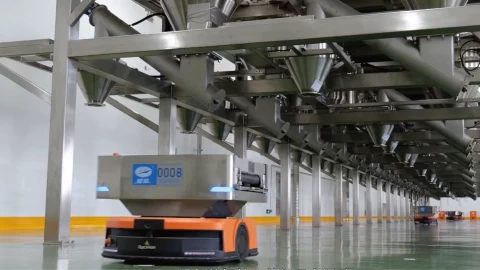
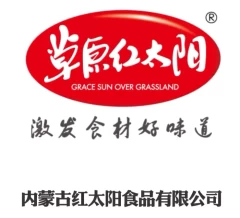